Following on from the successful re-wheeling of the locomotive’s frames, our attention has been split between the manufacture of a brand new smokebox and the completion of the spring gear to enable the locomotives weight to be transferred on to the springs.
Locomotive Spring Gear
The original driving axle springs which were overhauled at Swindon works in the early 1990’s were recovered from storage and given a coat of protective paint. Unfortunately when examining them it was noted that 2 of the 6 springs are borderline serviceable as some of the spring leafs are considerably corroded, to almost half the original thickness. Why Swindon never changed these when they replaced others in the spring remains a mystery. I can only assume that the workforce remaining at Swindon works thought that the loco would only ever be puffing up and down a siding and never running any distance; they didn’t reckon on the GWSR being the successful 15-mile railway it is now! We had originally planned to have two spare springs in stock for future replacement, so these new springs when purchased will be put straight on to the loco to replace the life expired ones. If you are considering sponsoring a component, then please consider helping us purchase these items as they will now definitely be required sooner rather than later. Check out our component sponsorship list for details.
The GWSR workshop has very kindly made us new spring links to a modified design which will enable the weight distribution to be easily adjusted using large nuts on the bottom of the secondary spring boxes. The previously manufactured secondary rubber spring pads have been fitted in the housing and attached to the spring hanger brackets.
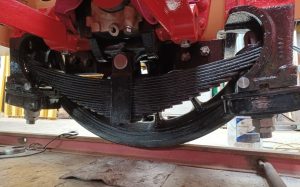
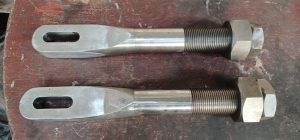
Smokebox
The original smokebox was so badly corroded that very few parts could be rescued from it for reuse. The superheater header brackets, self cleaning apparatus brackets, side handrail stations, and rear spacer ring which fit onto the boiler were the only serviceable parts. The smokebox assembly consists of over 30 different parts. We had already started machining some new parts, as part of our component sponsorship scheme but that process has been accelerated now that we need the parts to complete the assembly. We are very grateful to people who have sponsored the construction of these parts. Shown below is a selection of pictures of these new parts.
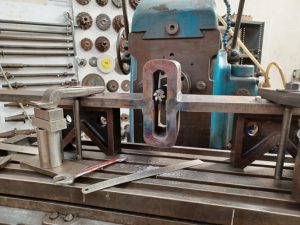
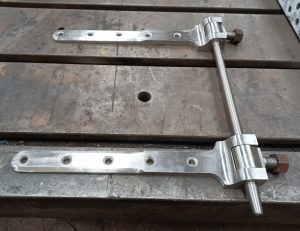
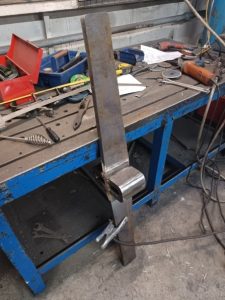
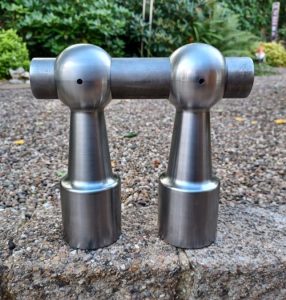
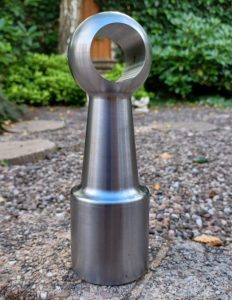
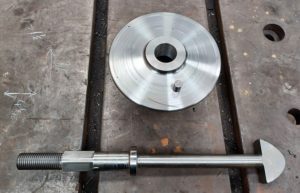
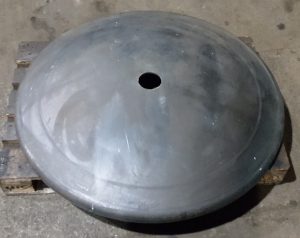
Although we have the drawings for the smokebox, it is surprising how many discrepancies are present between our original example and the drawings. A lot of care and attention has gone into marking out this difficult component. The problems arise from the dimensioning on the original drawings. To get the dimension you actually need, there is still a bit of arithmetic to do to, clearly the drawing office staff were not time served steel fabricators!
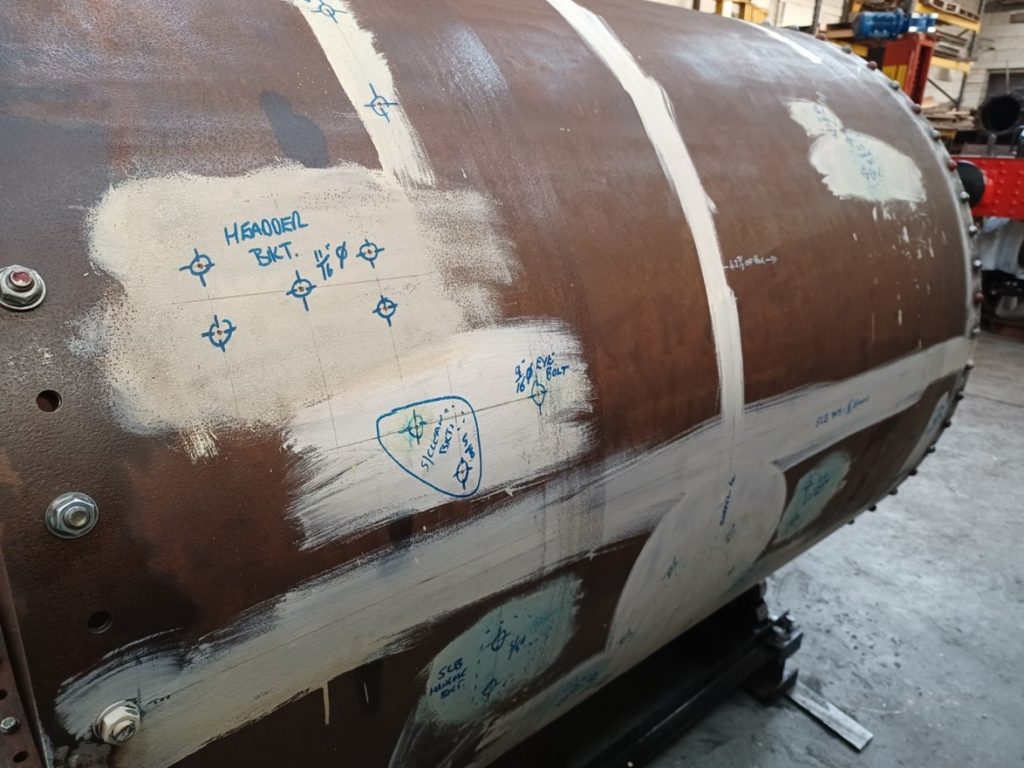
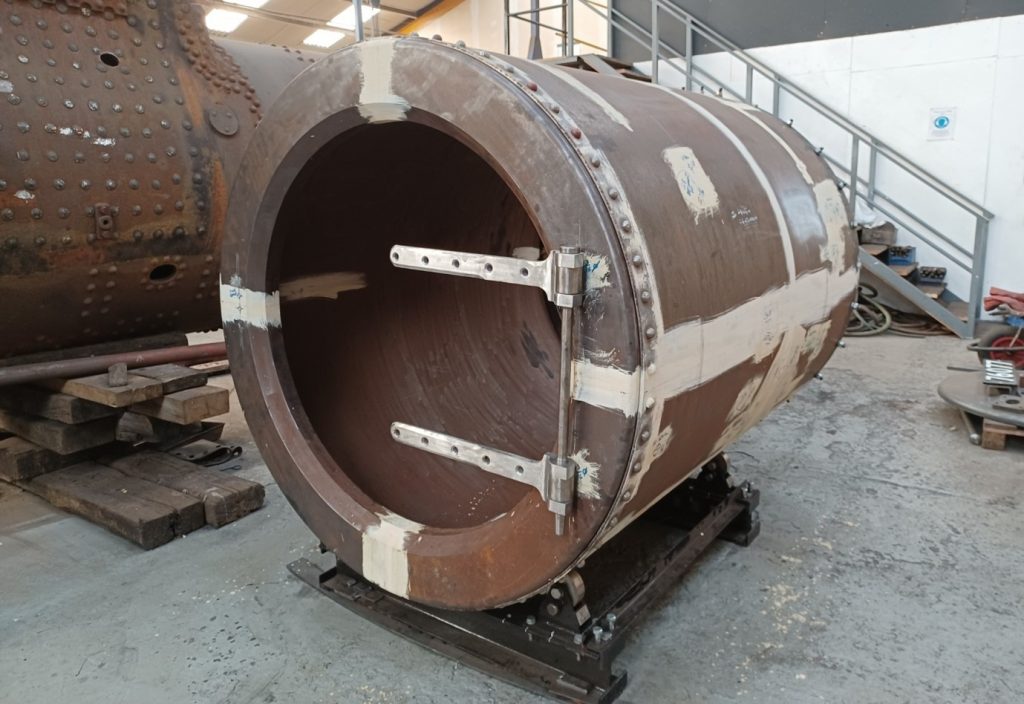
Work at Toddington
As well as the restoration work at LMS, our volunteers at Toddington have been busy. The coupling rods have been removed from long time storage and the hard work has begun to make them look like new again. The steel has quite a lot of pitting in it surface which must be ground out and the rods polished up. The bushes will also be pressed out and re-metalled and machined before refitting. The gradient pins and bushes which connect the two rod sections together just behind the driving axle are missing and new ones will have to be machined. I am very grateful to or volunteers who are working on the rods as it is a time consuming task, but one that will enhance the finished locomotive considerably.
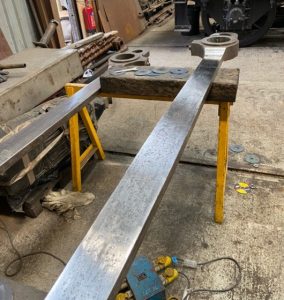
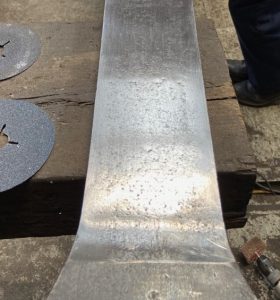
Our volunteers are highly valued, if you would like to get involved in the practical restoration either at Toddington or Loughborough contact the team, we will make you most welcome.
Finally the next 12months will see work concentrating on the chassis at Loughborough, new piston head castings have been ordered ready for when the cylinders are re-bored. The valves will be refitted and much of the motion will be refurbished and fitted where possible. The replacement reversing gear and the cab are also being worked on, so watch out for the next workshop update.
Andrew Meredith
Engineering Director