After the flurry of activity in July and September the last few months have been comparatively quiet, but that doesn’t mean we haven’t made progress in many areas.
At Loughborough the new brackets for the sand ejectors have been completed and fitted to the frames. This has allowed our previously machined sand ejectors to be fitted and the alignment with the wheels checked. Our volunteers have also been busy cleaning up the slide bars ready for eventual fitting once the cylinders are bored. On the subject of boring the cylinders, BREXIT has reared its ugly head and the brand new line boring equipment being purchased from Italy by LMS, has been stuck at UK Customs. No doubt reams of bureaucratic paperwork will have to be filled in before we see any sight of it. We are hopeful that the equipment will arrive by the end of December so we can get our cylinders bored early in 2023. Once the cylinders are bored then that opens up a significant amount of work with the pistons, valves, and the alignment and fitting of the slide bars and crossheads.
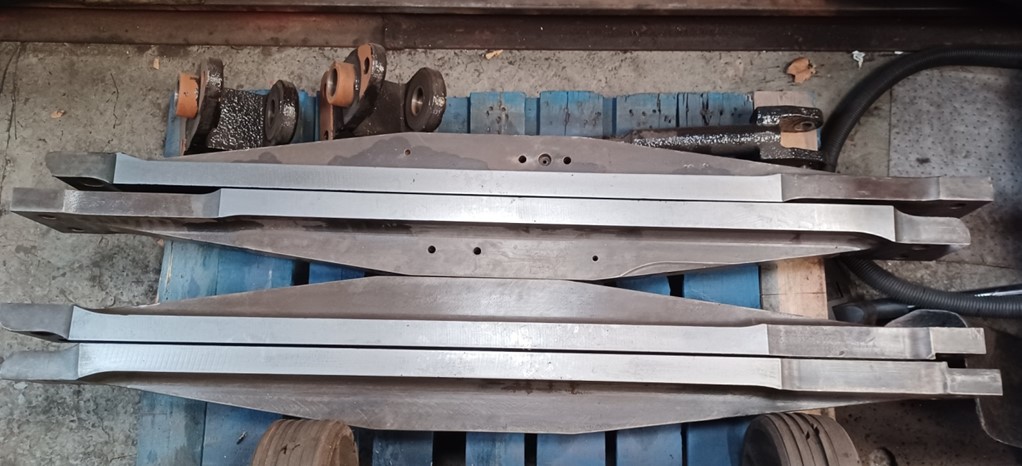
I have spent quite a few days forming pipe clips for the grease and oil lubrication pipe work. I have been amazed how long it has taken to make these clips (it’s a good job we weren’t paying someone to make them!). My attention has now turned to completing the bigger pipe clips for the vacuum, steam heat and sanding pipes. I am also now starting to fit the small bore grease pipe work that feeds grease from the blocks on the outside of the frames to the horns and the oil pipe work that feeds the axle box under keeps from the mechanical lubricator.
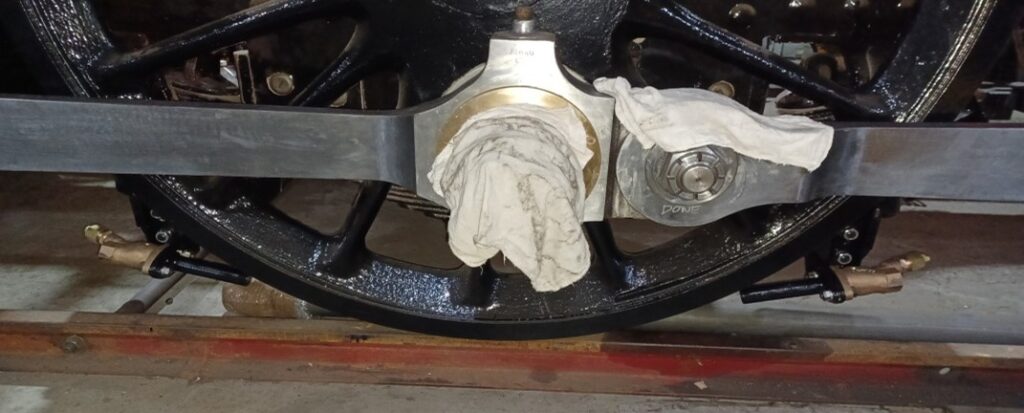
The cylinder cladding which Chris Hinton previously had made has been shot blasted and a coat of primer applied. The holes in the cylinders are being prepared ready to trial fit the cladding. Unfortunately many of the 3/8 set screws which hold the cladding on the cylinders have snapped off, so each one has to be carefully drilled out and re-tapped to size.
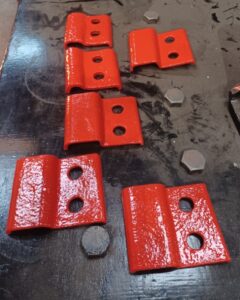
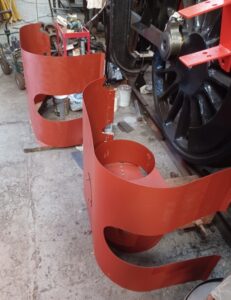
Other significant news is the delivery of the new reversing shaft screw and nut for the reversing shaft assembly. They were tricky parts to machine as the thread is a LH Acme twin start and the drawings specified a close fit between nut and shaft with minimum end float. These parts have been made by Statfold Engineering and have been finished to a very high standard. The next job is to assemble these together with all of the parts which were made in the GWSR workshop which will complete the reversing screw assembly. This can then be fixed to the frames at the side of the reversing shaft and the sheet metal protective covers rolled and welded together.
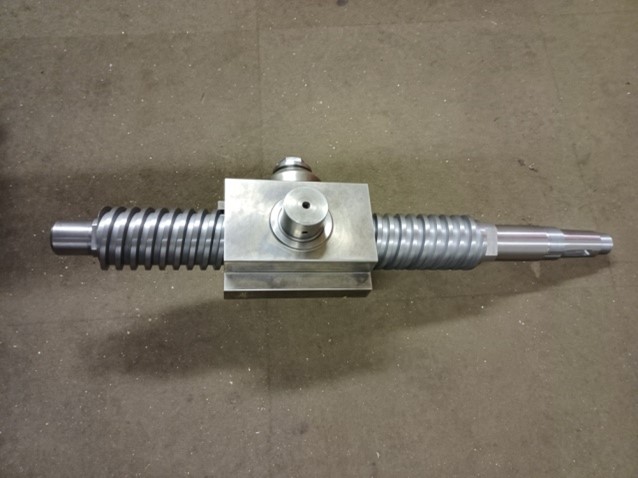
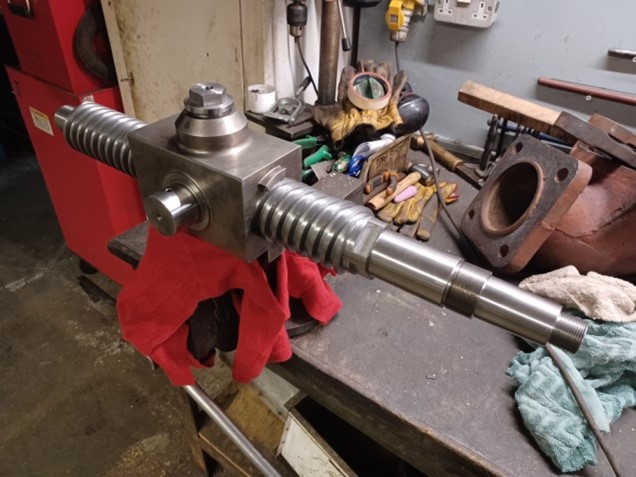
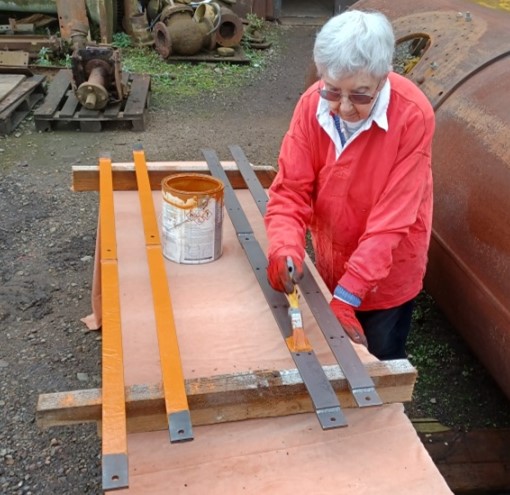
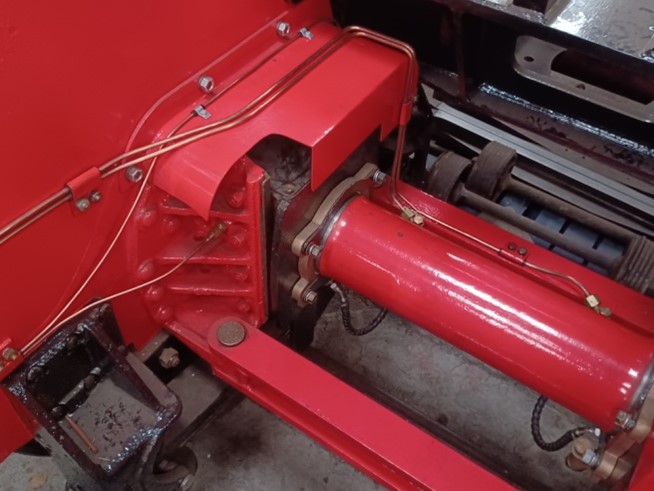
At Toddington the steam brake elbow fittings have been machined in the workshop and the two new atomiser castings have been started. After a plea for more work a selection of drawings and materials have been supplied for various parts to machined in the New year. Items include the firebox door runners, more brake gear pins and bushes and cab roof ventilator handles and catches.
Our volunteers in the yard at Toddington have been busy cleaning up and painting all the new firebox crinolines in preparation for fitting them to the boiler. Unfortunately, we are still waiting for the boiler to be extracted from its current position to enable work to be started, it is currently trapped in, by a set of diesel bogies which will hopefully be moved very soon. Work also continues with polishing up the valve gear removing decades of corrosion ready for eventual refitting.
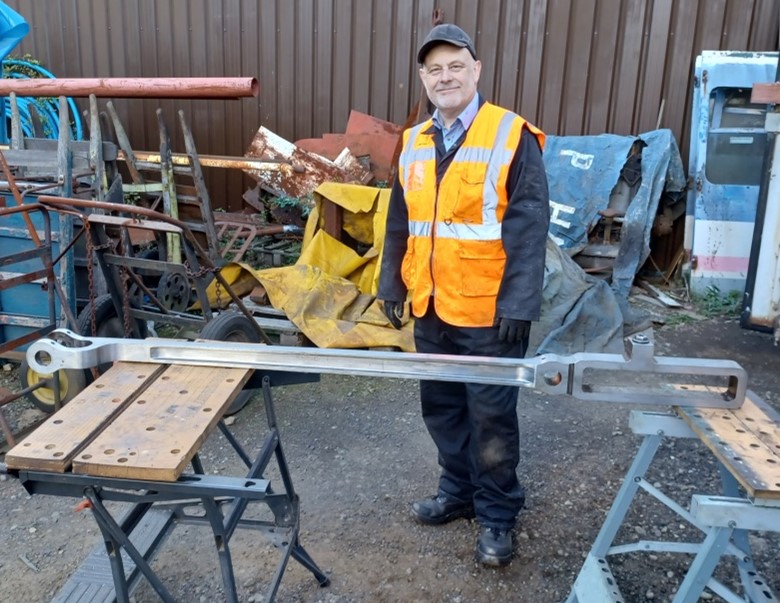
Can I take this opportunity to thank all our volunteers for their hard work and our supporters for continuing to finance the project, if you are considering either buying shares or volunteering with us then please make 2023 the year you do it. Only with your help will we achieve our 2026 goal.
Merry Christmas and a Happy New Year
Andy Meredith