05 February 2025: Work on the overhaul of the boiler of Standard Class 4 2-6-0 no. 76077, owned by Toddington Standard Locomotive Limited (TSLL) for eventual use on the Gloucestershire Warwickshire Steam Railway, has started in earnest – however an NDT (Non-Destructive Testing) examination has revealed additional unexpected problems.
When the boiler arrived at the Devon workshops of Leaky Finders Ltd, planned work immediately started with removal of the front tube plate, which is to be replaced. In addition, the front parallel ring of the barrel is to be replaced and the boiler has been inverted to complete removal of the ring, while most of the foundation ring rivets have also been removed. Part of the corroded firebox throat plate has also been cut out.
The boiler has also undergone a full NDT examination which has revealed that the steel from which the boiler was manufactured has laminations present which is of concern, particularly where areas need to be welded, for example carrying out patch repairs.
Explains Andrew Meredith, engineering director of TSLL: “In January, our chairman, Chris Irving and I visited Leaky Finders along with the NDT specialists and the boiler inspector to agree a way forward. While the lamination issues are not in themselves a show-stopper, it does mean that the work to return the boiler to working order will be much more extensive than we, or indeed Rory Edwards at Leaky Finders, originally thought.”
When a steel ingot is rolled several times to form the required size and thickness of metal plate, impurities (such as small deposits of slag) can end up as linear pockets within the steel, known as laminations.
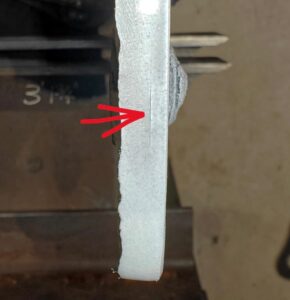
Continues Andrew Meredith: “While these laminations may not in themselves be a major issue – and, after all, the boiler has performed perfectly well though its BR career – they become a significant problem when patches need to be welded in to replace corroded material. Welding near a lamination can result in cracks forming, thus weakening the metal.
“Unfortunately, our boiler was completed at Darlington in 1952 at a time when steel quality was sometimes poor. Of course, the technology to identify these laminations was not available then. The discovery means that we will have to remove much more of the firebox steelwork than planned. In the process it also means that over 400 perfectly serviceable copper stays will have to be sacrificed.”
The NDT process also identified that many of the original Monel metal stays which are within the upper part of the firebox are broken or flawed and will have to be replaced, while a few rows of crowns stays have also been found to need replacing, due to excessive wastage of their heads in the firebox.
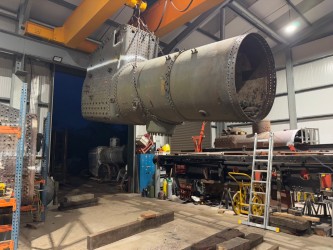
Chris Irving, TSLL’s chairman adds: “Of course this wasn’t the ‘Happy New Year’ we were expecting and it will significantly increase the cost of the boiler overhaul. It is also likely to push back our aspirational date for seeing the locomotive steam again. On the positive side, however, this additional work will build in additional longevity to the boiler and reduce the amount of work that we might otherwise need to do following the engine’s first ten years in service.”
TSLL will be stepping up its fund-raising effort to meet these unwelcome additional costs (which have yet to be confirmed) and the company will welcome new shareholders to help keep the overhaul on track.
Concludes Chris Irving: “We are deeply grateful to all of our shareholders. We certainly wouldn’t be at this stage in our, frankly, very rapid progress without the huge engagement and financial support that has been forthcoming from so many people, many of whom have joined our volunteer working parties too.
“We owe them all the commitment to deliver a locomotive in working order as soon as we possibly can and that very much remains the focus of our team.”
Inf0rmation about the locomotive and how to become involved can be found at www.standard76077.com; calling 07775 566 555 or email info@standard76077.com.
Article and Interviews by Ian Crowder – TSLL Marketing Director